5 Best Practices for Managing Construction Equipment Efficiently
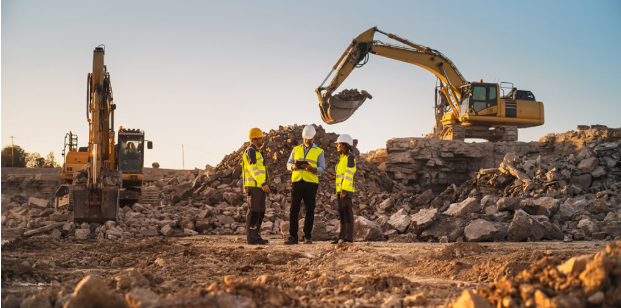
Managing construction equipment the right way can save time, reduce costs, and improve safety on the site. Equipment breakdowns, unexpected repairs, and inefficient use can slow down projects and increase expenses.
That’s why following the best practices in construction equipment management is essential. Here are five proven ways to make sure your construction equipment is well-maintained and used efficiently.
1. Keep a Strict Maintenance Schedule
Regular maintenance is the key to keeping construction equipment in good shape. Ignoring routine checkups can lead to expensive repairs and unexpected breakdowns that delay projects. Simple tasks like checking fluids, lubricating parts, and inspecting for wear and tear can extend the life of your machines.
It’s best to follow the manufacturer’s guidelines and schedule maintenance at fixed intervals. Digital tracking systems can help you stay on top of this by sending reminders and keeping records. A well-maintained machine performs better, lasts longer, and keeps workers safe.
2. Train Operators for Efficiency and Safety
Even the best equipment won’t be useful if operators don’t know how to use it properly. Many accidents and machine failures happen because of a lack of training. When workers know how to handle equipment correctly, they can prevent damage and improve work efficiency.
Regular training sessions help operators understand safety rules, operating techniques, and troubleshooting methods. Investing in training reduces mistakes, lowers fuel consumption, and prevents unnecessary wear and tear.
3. Use Cranes Smartly to Avoid Accidents
Cranes are essential for lifting and moving heavy materials, but they can be dangerous if not handled properly. Overloading, improper setup, and poor communication can cause serious accidents. A well-maintained crane and a trained operator are crucial for safe and smooth lifting operations.
Before using a crane, always check the load capacity and inspect the rigging equipment. Operators must follow safety protocols, communicate clearly with the ground team, and ensure proper weight distribution. Using cranes smartly not only prevents accidents but also speeds up construction work.
4. Make the Most of Earth Moving Equipment Rental
Buying heavy machinery isn’t always the best choice, especially for short-term projects. Therefore, earth moving equipment rental can save money, reduce maintenance costs, and provide access to the latest technology. Companies offering rentals often maintain their equipment well, so you get machines that are in top condition.
Before renting, check the equipment’s condition and ensure it fits your project needs. Renting allows flexibility—you can get the exact machine required for a specific task without worrying about storage or long-term costs.
5. Track Equipment Usage and Performance
Keeping track of how equipment is used can help in making better decisions. Some machines may be overused, while others might sit idle for too long. GPS tracking and telematics technology allow managers to monitor usage, fuel consumption, and machine health in real time.
Analyzing this data can help in scheduling maintenance, reducing fuel waste, and improving productivity. When you know exactly how each machine is performing, you can plan better and avoid unnecessary costs.
Conclusion
Managing construction equipment the right way leads to smoother operations, fewer breakdowns, and cost savings. Regular maintenance, operator training, smart crane usage, renting when needed, and tracking performance can make a big difference.
By following these best practices, construction managers can ensure that their equipment stays in top shape and projects run efficiently.